Streamlining Procurement and Inventory Management Leads to Increased Productivity
Challenge
In addition to planning a relocation to a new headquarters to accommodate growth, a biotechnology company wanted to take the opportunity to streamline tasks and increase efficiency of its operations. A review had determined that scientists, technicians, and other skilled employees were wasting nearly 5,000 hours a year on ancillary tasks such as inventory management.
To make matters worse, the lost productivity from these tasks was costing the company more than $649,000 annually, with losses from excess inventory across campus amounting to an additional $146,500. What adjustments could the company make to streamline these ancillary processes at their new headquarters?
Solution
The company engaged a Avantor Services Lean Six Sigma Business Process Consultant to help consolidate necessary tasks into new roles. Working closely with an internal team, the consultant coordinated an extensive review of the current process, particularly as it related to the management of lab supplies. Prior to this review, there were many employees involved in the purchasing, inventory, stocking, and accounts payable processes; afterward, one employee was responsible for coordinating these tasks. This allowed the company to simplify and standardize all of these processes to reduce waste, cut costs, and recapture time for scientists to focus on research. The solution also included a metrics package to help managers drive inventory reduction.
Result
Streamlining the standardizing the procure-to-pay process created more than $276,000 in direct labor and inventory cost savings—factoring in the lost productivity of skilled employees nearly triples that value to just over $796,000.
The value uncovered through this project led the company to leverage the Avantor Services consultant for continuous improvement. The consultant found that additional value could be found through improving the company’s approach to glasswash, chemical management, and mailroom services. Partnering with industry-leading chemical tracking software and MSDS management software, the consultant was able to design a solution that provides additional value of more than $553,000.
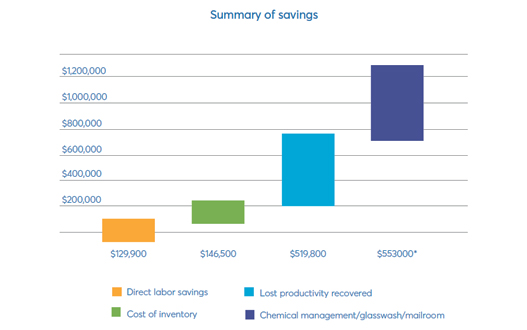
Figure 1. By freeing up time for skilled employees to focus on core activities, the company’s savings nearly tripled. Extra value was added by changes to the chemical management, glasswash, and mailroom services.
*Projected Value